In today's business environment, the importance of a centralized procurement process for equipment to enterprises and organizations is self-evident. It can not only reduce procurement costs, but also ensure the quality of equipment and the stability of supply. So, what is the equipment centralized procurement process?
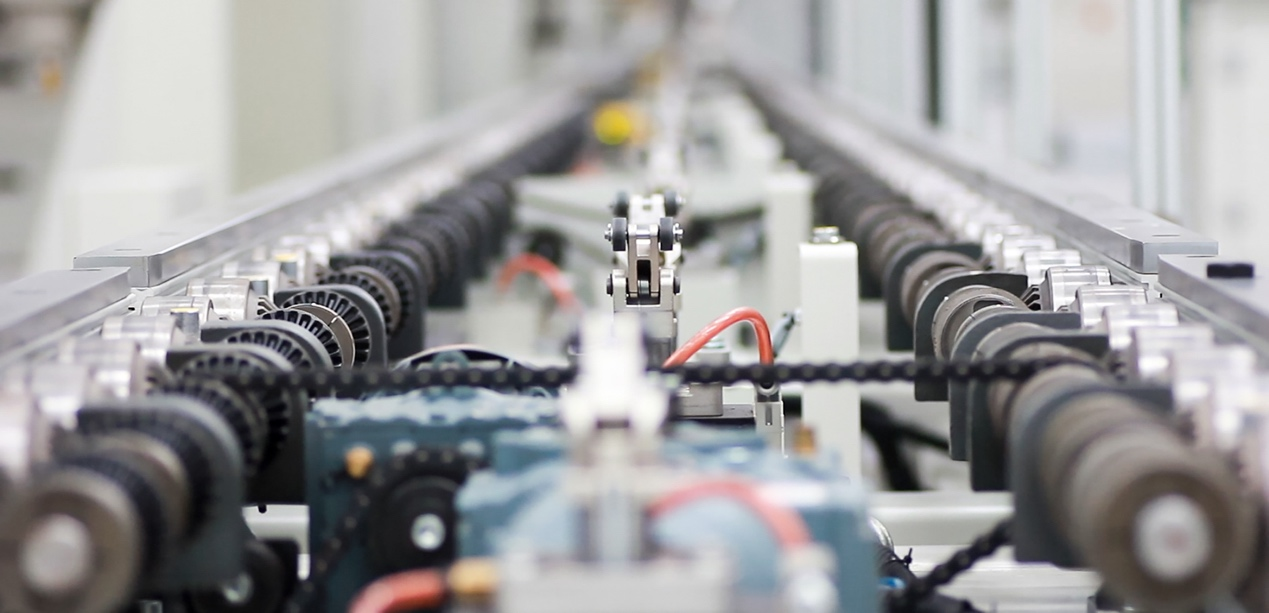
1. Demand Determination
This is the most critical step in the equipment centralized procurement process. Each department submits an application for the equipment centralized procurement process according to actual business needs, and clarifies the specifications, models, quantities, technical requirements, etc. of the required equipment. The procurement department summarizes, analyzes and integrates these requirements to ensure the rationality and accuracy of the requirements.
For example, the production department of a manufacturing company may need new machine tools to improve production efficiency, while the R&D department may need high-precision testing instruments. Then, the procurement department needs to fully communicate with these departments to understand their specific needs in order to develop a comprehensive equipment procurement process plan.
2. Market Research
After clarifying the requirements, the purchasing department begins to conduct market research. At this stage, it is necessary to collect information about potential suppliers and fully understand the price, quality, characteristics, after-sales service, etc. of similar equipment on the market.
Information can be obtained through online searches, attending industry exhibitions, and asking professionals. At the same time, you can also ask existing suppliers to find out whether they can provide the required equipment. Through market research, the purchasing department can grasp market trends and provide a basis for subsequent equipment procurement process decisions.
3. Formulate A Procurement Plan
Based on the actual situation and the results of the market research report, the procurement department shall formulate a detailed procurement plan. The procurement plan shall include the procurement method (such as open bidding, invitation bidding, competitive negotiation, etc.), bid evaluation criteria, contract terms, etc.
For example, if an open bidding method is adopted, the procurement plan shall specify the release channel of the bidding announcement, the bid deadline, the bid opening time and location, etc. The bid evaluation criteria shall be formulated based on the technical requirements, price, after-sales service and other factors of the equipment to ensure that a supplier that better meets the needs of the enterprise can be selected.
4. Supplier Selection
You can invite suppliers to bid or quote according to the equipment centralized procurement process determined by the procurement plan. The procurement department reviews the suppliers' bidding documents or quotations and selects qualified suppliers based on the bid evaluation criteria.
During the review process, we should not only pay attention to price factors, but also consider the supplier's reputation, product quality, after-sales service, etc. A comprehensive evaluation can be conducted by checking the supplier's corporate qualification certificate, customer feedback, field investigation, etc.
5. Contract Signing
Sign a purchase agreement with the selected supplier. The contract should clearly state the equipment specifications, models, quantity, price, delivery date, quality standards, after-sales service and other contract terms to ensure that the interests of both parties are effectively protected.
Meanwhile, the purchasing department should maintain close communication with suppliers to promptly resolve problems that arise during contract execution.
6. Equipment Acceptance
After the equipment arrives, the purchasing department organizes relevant departments to conduct acceptance. The acceptance content includes the appearance, quantity, specifications, performance and other aspects of the equipment to ensure that the equipment meets the contract requirements.
If you encounter quality problems with the equipment or if it is inconsistent with the contract, you should negotiate with the supplier on time and ask the supplier to make corrections or replacements.
7. Payment Settlement
After the equipment procurement process is accepted, payment settlement will be made by the payment method agreed in the contract.
Although the equipment centralized procurement process is complicated, as long as the steps are strictly followed, the procurement can be ensured to be efficient, transparent and fair. SUMEC International Technology Co., Ltd. was established in March 1999 and is affiliated with China National Machinery Industry Corporation. Its equipment centralized procurement services have rich experience and professional capabilities. The company has accumulated tens of thousands of domestic and foreign equipment and bulk resource suppliers, and can quickly respond to customer procurement needs; with rich industry experience, it can provide customers with a package of centralized procurement solutions, and the butler-style service makes you worry-free and assured!