

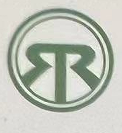


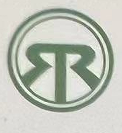


Product information
The specific process of picking charging pile shell
1, design: first of all, according to the product design requirements, the design of the shell. This includes determining the requirements in terms of shape, size, style and function. The design stage may involve the use of computer-aided design software (CAD) for three-dimensional model design and rendering.
2、Material Preparation: Selection of applicable materials for use in the production of charging piles Common materials include metal (e.g. aluminium alloy, steel) and plastic (e.g. polycarbonate, polypropylene). The material should meet the product requirements, such as strength, weather resistance and waterproof performance.
3, manufacturing process: according to the design requirements, using the appropriate manufacturing process for shell production. Common manufacturing processes include:
Metal shell: using CNC machine tools for cutting, drilling, stamping and other processes, the metal plate processing into the required shell parts. Then shearing: using a shearing machine to cut the material to the required size.
Stamping/Cutting: Plastic deformation of the material using a mould to achieve a predetermined shape and size.
Bending/Curling: The material is bent at a specific angle by means of a bending machine.
Welding: Separate sheets or parts are joined together by welding.
Surface treatment: Including painting, plastic spraying and anti-rust plating to enhance the product. Parts are assembled into a complete shell structure by welding, riveting or bolting.
Plastic shell: Usually adopts injection moulding process. Firstly, the mould of the shell is made according to the design requirements. Then, the plastic granules are heated in the injection moulding machine, the molten plastic is injected into the mould, and after cooling and curing, the plastic parts are taken out to form the shell parts
4、Surface treatment: Surface treatment is carried out according to the requirements to improve the appearance and durability of the shell. Common surface treatment methods include spraying, plating, anodising and polishing. These methods can increase the corrosion resistance, wear resistance and aesthetics of the shell.
Good external
5、Assembly and commissioning: the made shell is assembled with the internal components of the charging pile. This includes installing electronic equipment, connecting wires, installing control panels and displays, and so on. After the assembly is completed, functional testing and debugging are carried out to ensure the normal operation of the charging pile.
6、Quality Inspection: Conduct quality inspection on the finished charging pile shell, including appearance inspection, size measurement, function test and so on. Ensure that the shell meets the design requirements, and meets the relevant quality standards and certification requirements.
7、Packaging and factory: pack the charging pile which passes the quality inspection, to protect the shell from damage during transport and handling, then, the charging pile will be factory ready








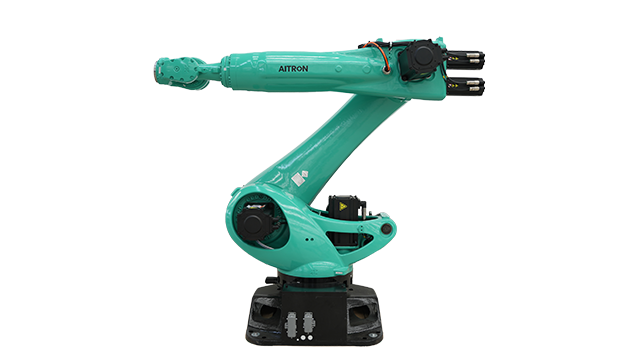
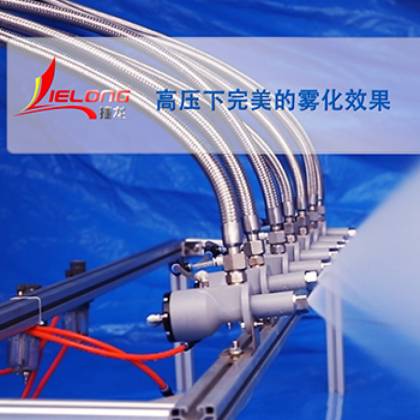
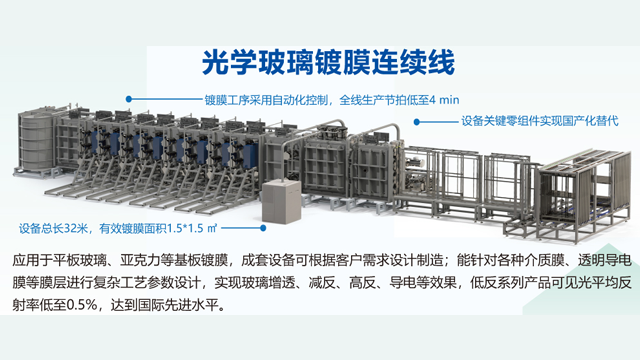
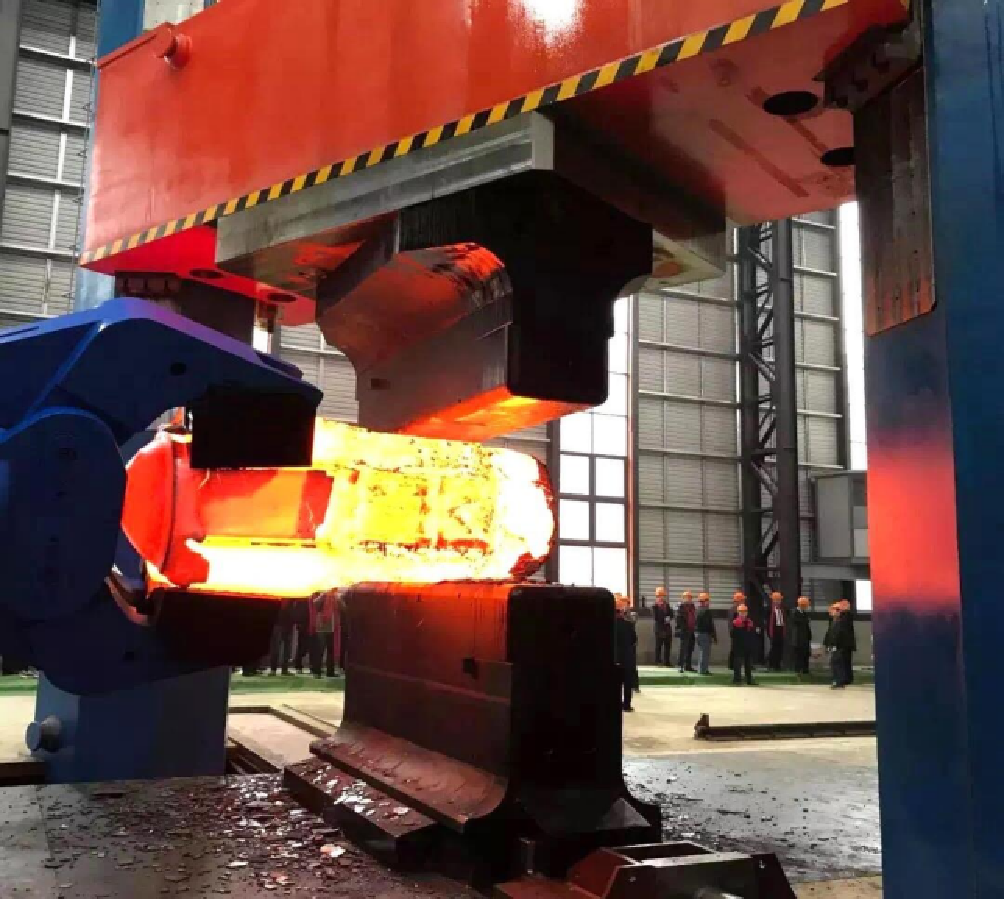
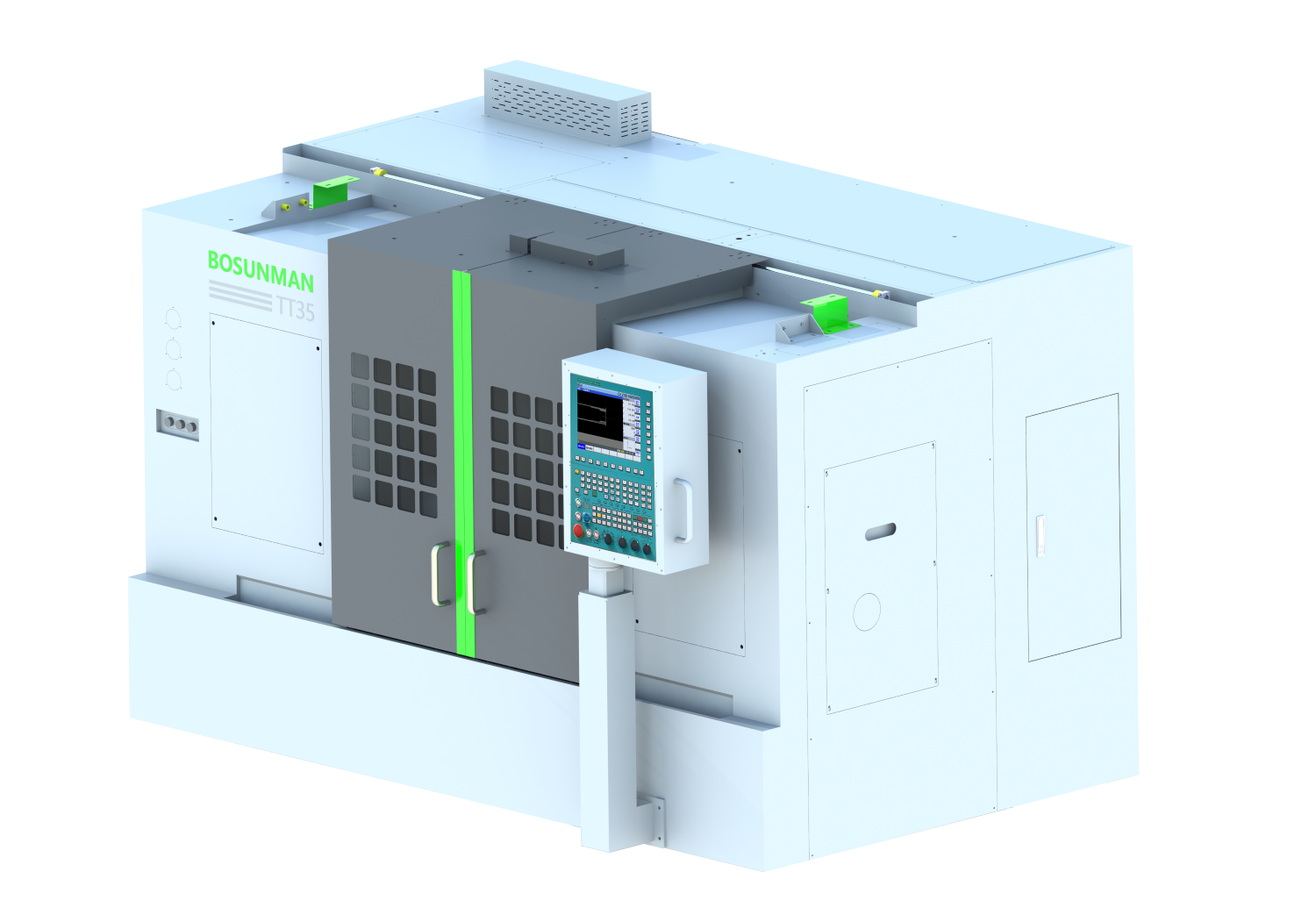
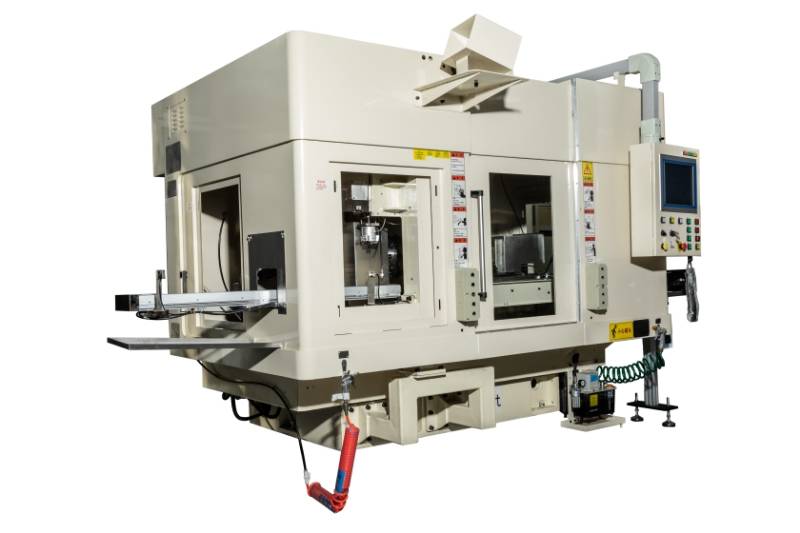
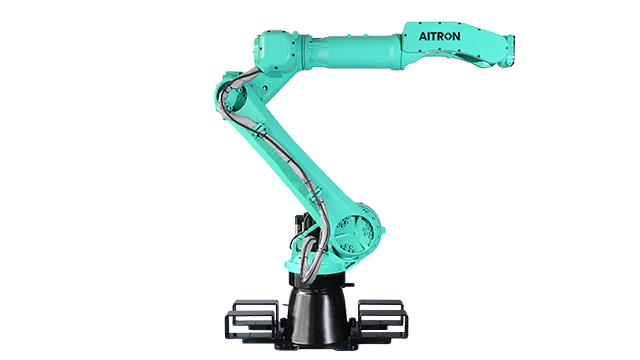
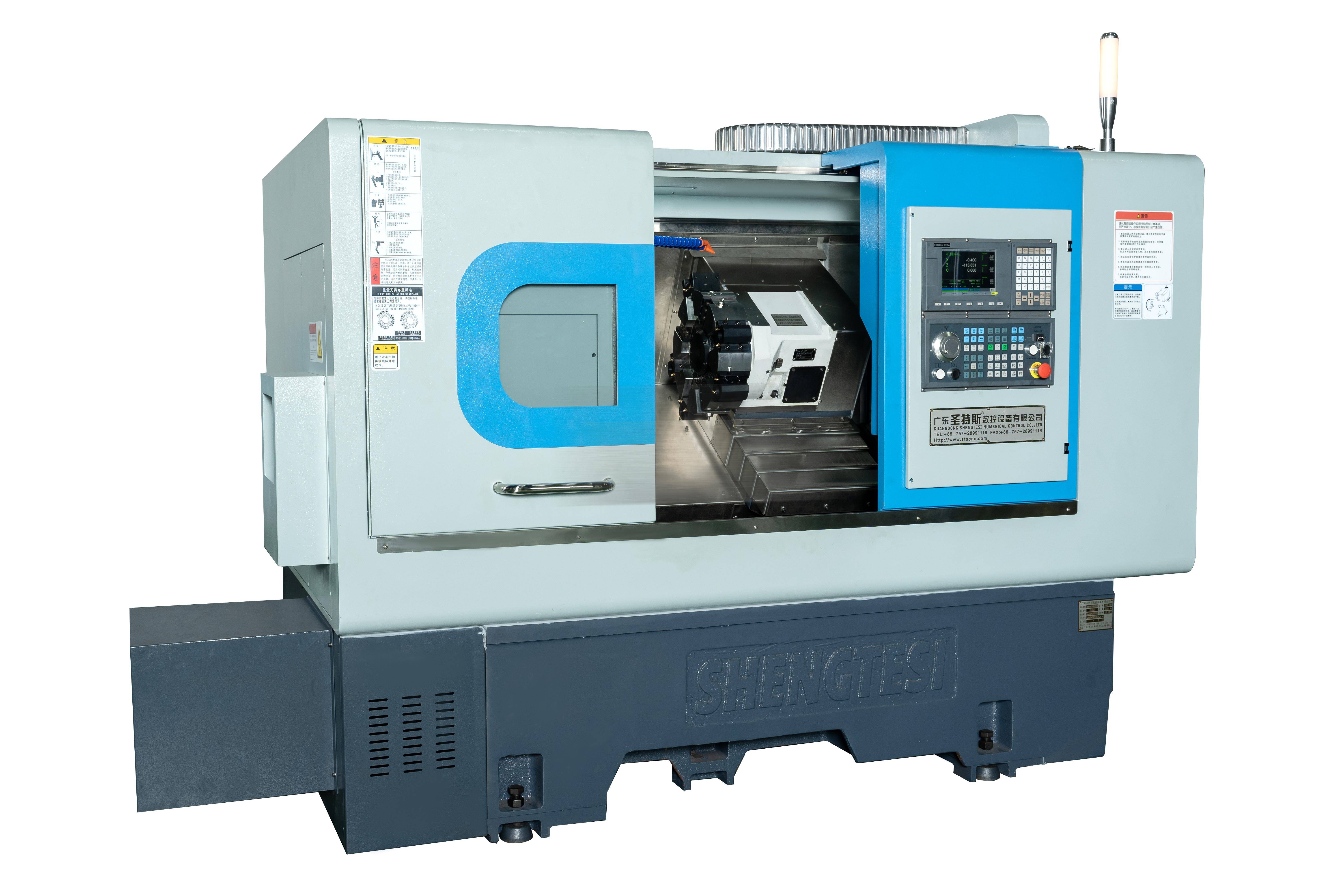
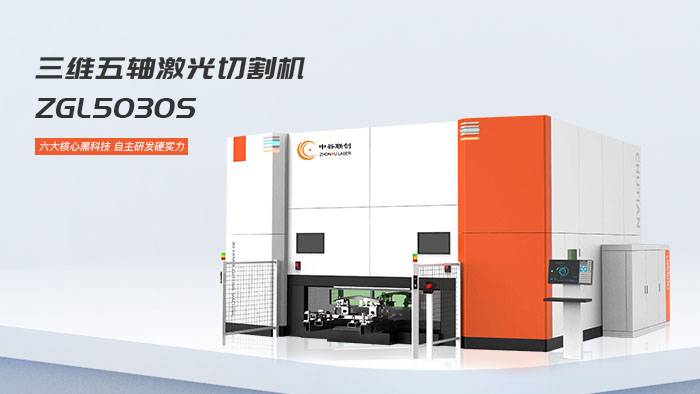
