



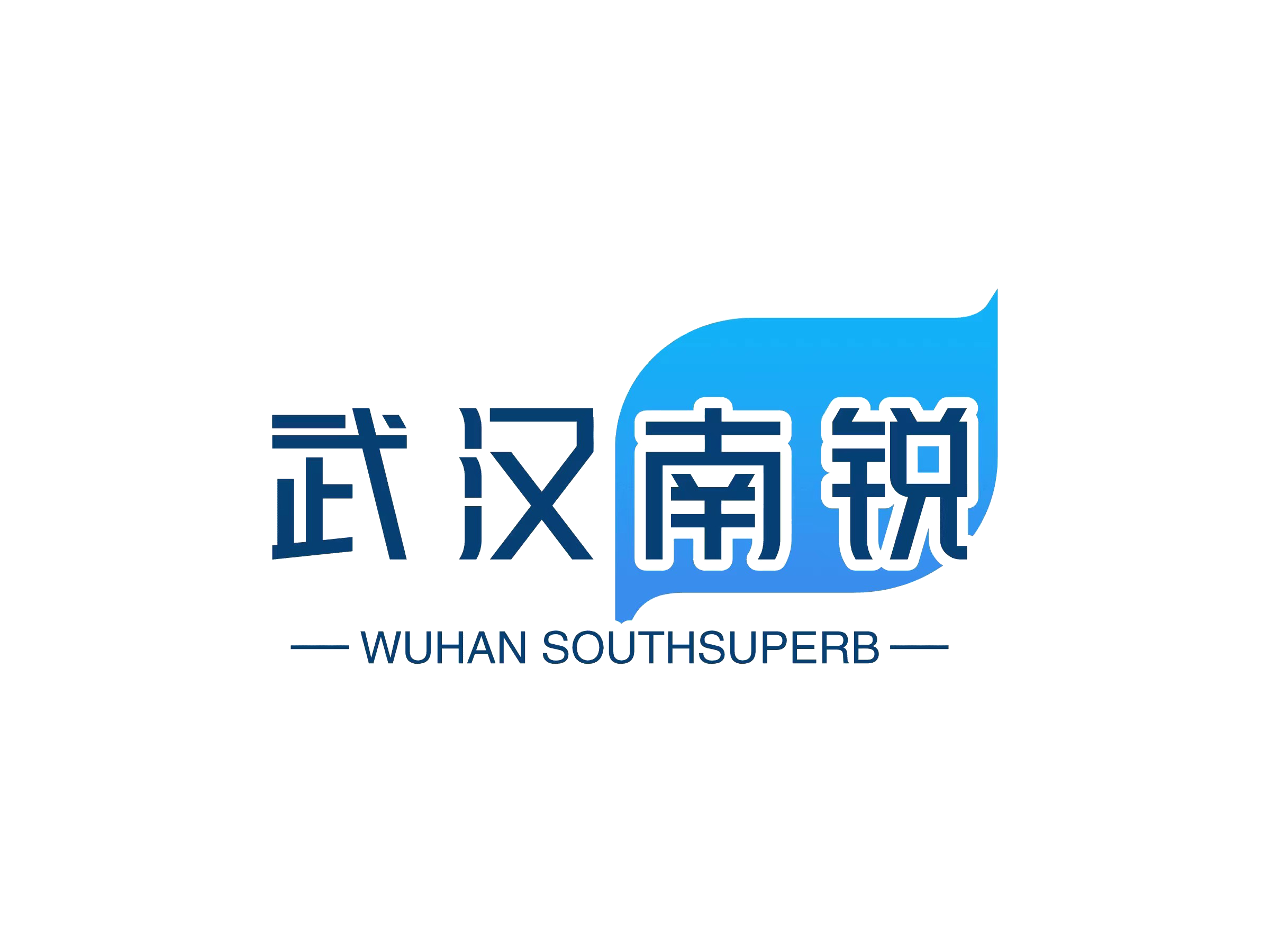


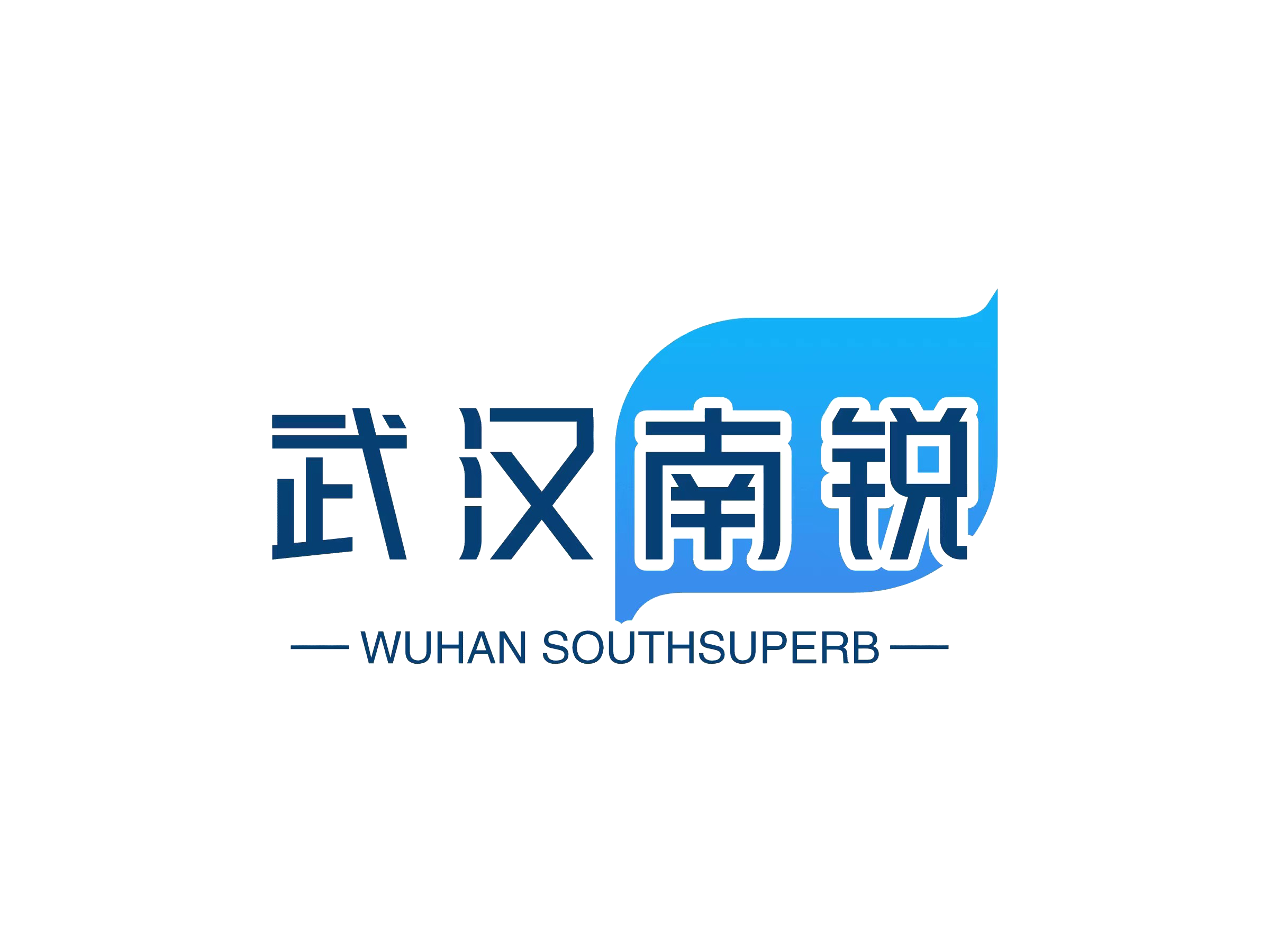


Product information
Sulfur is one of the harmful elements in molten steel, which can cause hot brittleness and reduce the mechanical properties of steel. Not conducive to the corrosion resistance and weldability of steel. Pre treatment of molten iron mainly refers to the desulfurization treatment of molten iron before entering the converter in steelmaking production. The general pretreatment of molten iron refers to the three de treatments including desulfurization, desilication, and dephosphorization of molten iron. Iron desulfurization is a technology developed in the 1970s for iron treatment, which has become an important component of optimizing the process flow in modern steel and iron enterprises.
2. Advantages and system features
a) Iron contains a large amount of reducing elements such as silicon, carbon, and manganese. When using various desulfurizers, the desulfurizer has less burning loss and high utilization rate, which is beneficial for desulfurization.
b) The carbon and silicon in molten iron can greatly increase the activity coefficient of sulfur in molten iron, improve the thermodynamic conditions for desulfurization, and make sulfur more easily desorbed to lower levels.
c) The low oxygen content in molten iron increases the distribution coefficient of sulfur in slag iron, which is beneficial for desulfurization.
d) The low temperature of molten iron processing results in a relatively long lifespan for refractory materials and processing equipment.
e) The cost of desulfurization of molten iron is low, such as removing one kilogram of sulfur in blast furnaces, converters, and external refining devices, which are 2.6, 16.9, and 6.1 times the cost of desulfurization of molten iron, respectively.
f) The changes in the composition of molten iron during the process of desulfurization outside the furnace have a smaller impact on the final steel grade composition than the changes in the composition of molten steel during steelmaking or external treatment of molten steel.
g) The use of molten iron desulfurization can not only reduce the burden on the blast furnace, lower the coke ratio, decrease the slag amount, and improve productivity, but also eliminate the need for large slag and high alkalinity operations in the converter for desulfurization, as desulfurization is quite difficult under high oxidation slag conditions in the converter. Therefore, desulfurization of molten iron has become an important means of optimizing the process flow in modern steel industry, and is the main measure to improve steel quality and expand varieties.
3. Process flow
The iron desulfurization system generally includes: iron transportation and tilting system, injection system (single injection of granular magnesium), slag removal system, dust removal system, feeding system, and automatic air control system.
Process model introduction: The purpose of the process model is to ensure the smooth operation of the injection process, using the least amount of magnesium desulfurizer while achieving the target sulfur. The consumption of magnesium desulfurizer is influenced by more than ten factors. In actual industrial operation, only five main variable factors are input into the process model, namely the original sulfur of the molten iron, the original temperature of the molten iron, the amount of processed iron, the target sulfur, and the metal magnesium content of the granular magnesium. The process model calculates the magnesium injection speed at different time periods of the furnace, the gas loading capacity at different time periods of the furnace, the total magnesium injection time, and the total consumption of magnesium desulfurizer, and stores them in the computer. At the same time, the above values are displayed on the LCD screen. The amount of magnesium injection speed depends on the speed of the variable frequency motor of the rotor feeder controlled by the computer, and the gas loading capacity is matched with the high-precision flow meter by the opening of the flow control valve controlled by the computer. At the same time, in order to increase the flexibility of the process operation, the magnesium injection speed, gas loading capacity, and initial sulfur can be manually interfered with in automatic mode. When the magnesium injection speed is manually interfered with, the magnesium injection speed can be adjusted between 4-12kg/min, and the total magnesium injection time will vary accordingly; When there is human interference with the gas carrying capacity, it can be adjusted between 30-170Nm3/h, and the total consumption of gas carrying capacity and magnesium desulfurizer will change accordingly.
4. Automated control system
a) The automation control system fully meets all the requirements of the process, works reliably, and is based on the level of new world achievements.
b) The process automation control system of the single blown granular magnesium iron desulfurization device adopts Siemens PLC to complete a series of automation tasks.
c) The automation control system of the molten iron desulfurization device can communicate data with other control systems in the factory (such as the secondary and tertiary systems of the steelmaking system) through its built-in Microsoft SQL Server database.








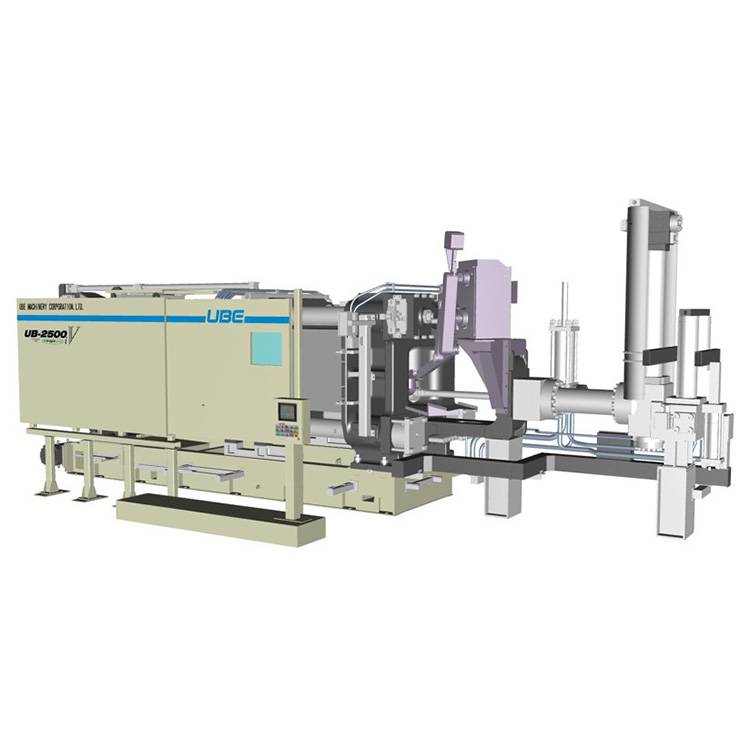
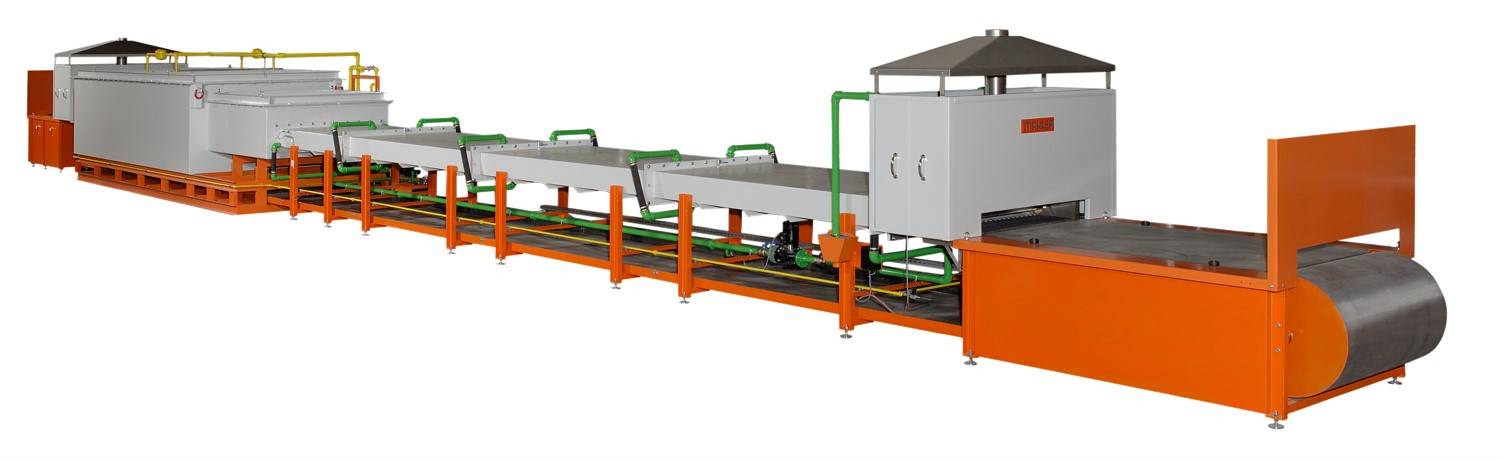
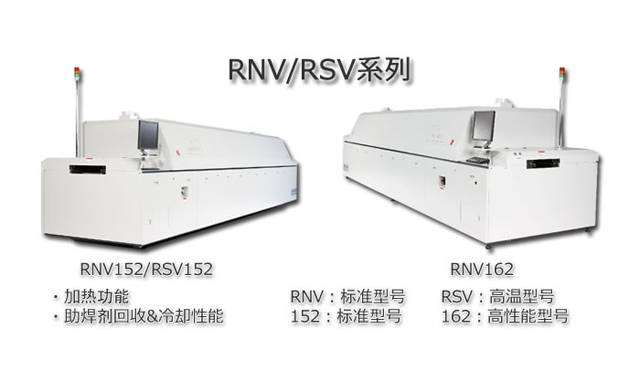
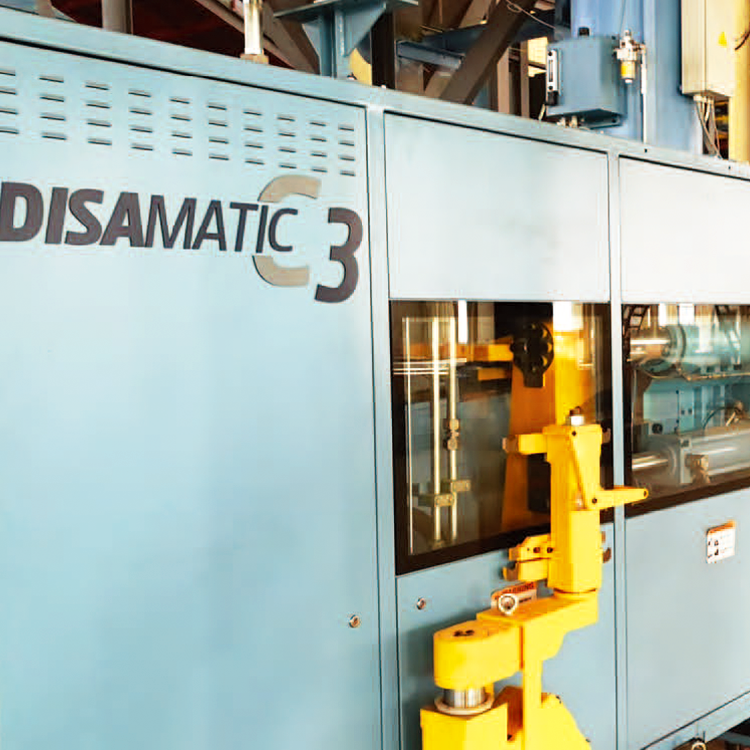
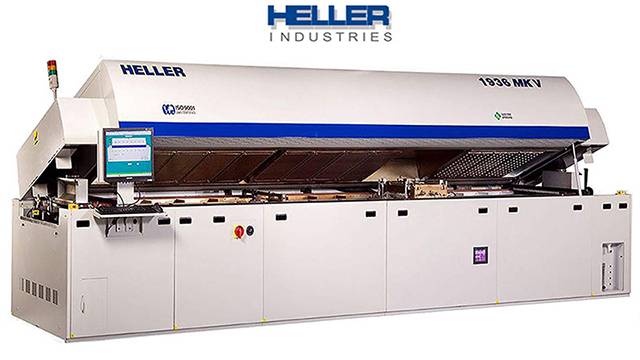
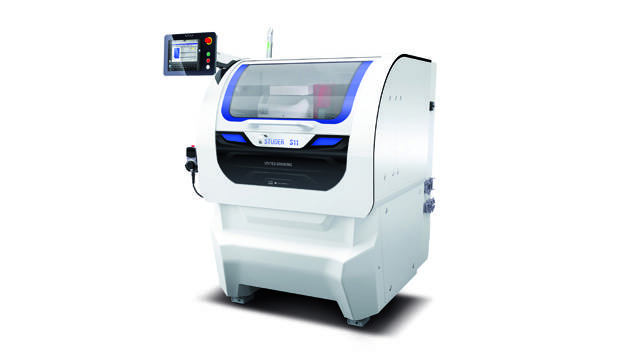
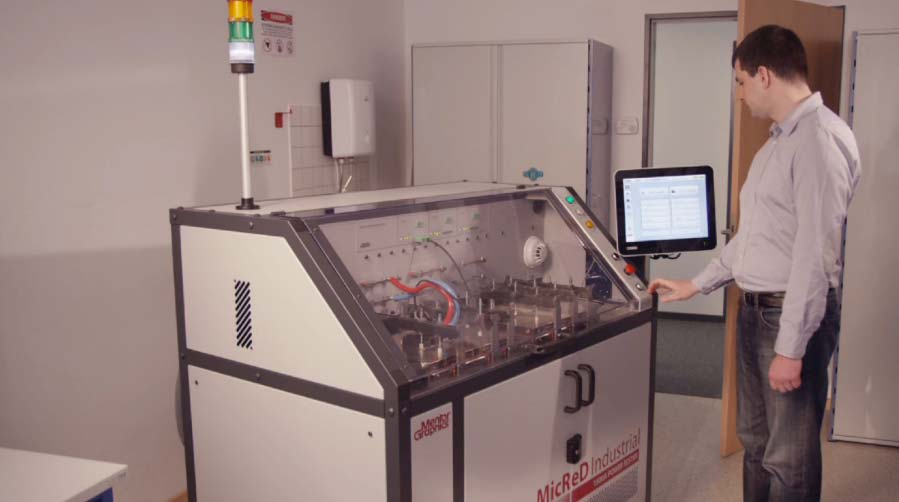
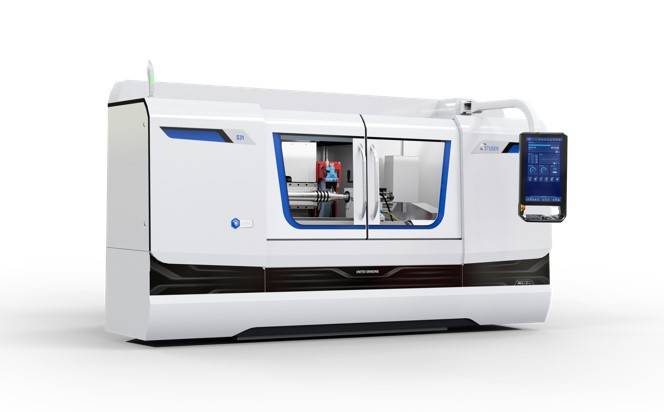
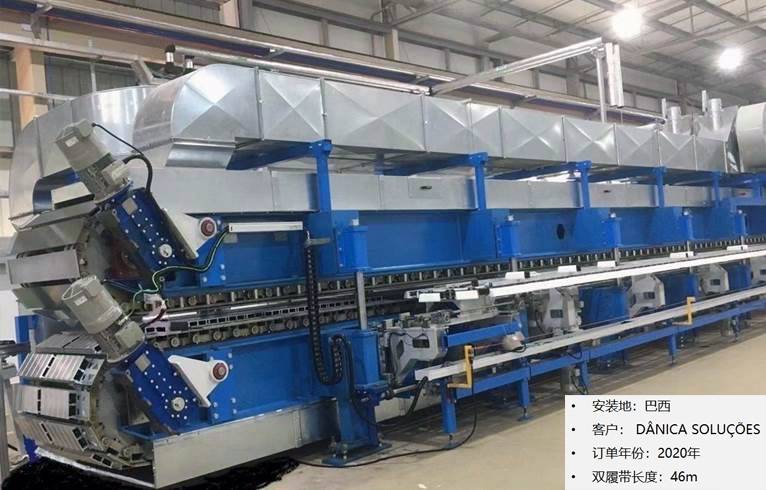
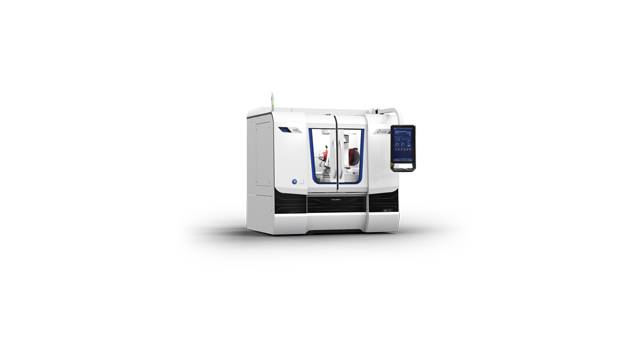