



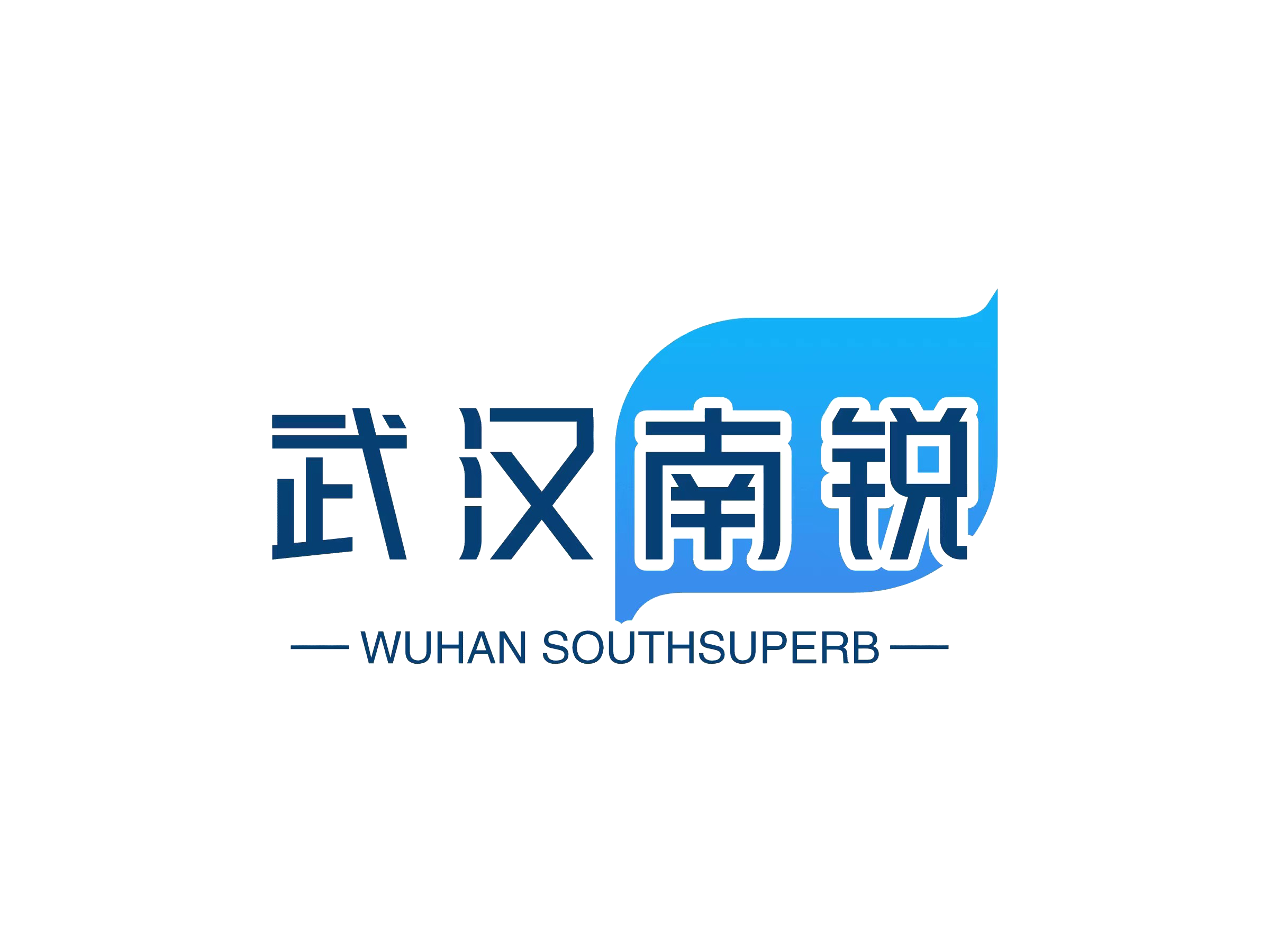


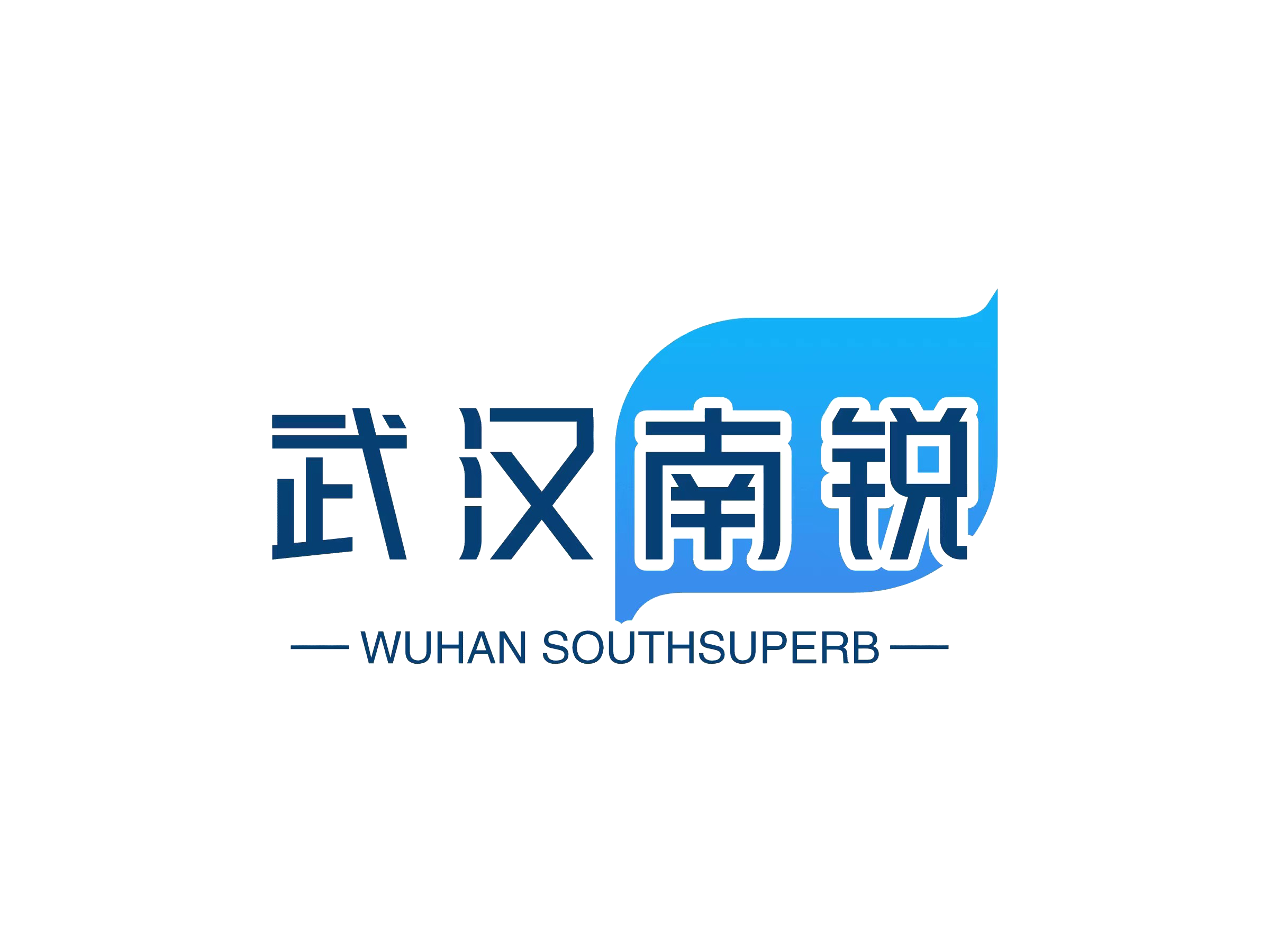


Product information
Basic Principle of Converter Steelmaking
The basic principle of converter steelmaking is to utilize the physical and chemical heat in molten iron. Inside the converter, oxygen or other oxidizing gases are blown in to oxidize impurity elements such as carbon, silicon, manganese, phosphorus, and sulfur in the molten iron, generating corresponding oxides that enter the slag, thereby obtaining steel water. Simultaneously, the heat generated during the oxygen blowing process melts the molten iron and added slagging materials, forming a molten bath. In the molten bath, by controlling the amount of oxygen blown and the type and quantity of slagging materials added, the composition and temperature of the steel water can be adjusted to meet the requirements of different steel grades.
Equipment for Converter Steelmaking
The converter is the primary equipment for converter steelmaking. It is a rotatable vertical furnace typically composed of components such as the furnace shell, furnace lining, furnace mouth, furnace hood, supporting ring, trunnion, and tilting mechanism. The furnace lining of the converter is usually made of refractory materials to withstand high temperatures and slag erosion. Air inlets are provided at the bottom or side of the converter for blowing in oxygen or other oxidizing gases. Additionally, the converter is equipped with a tapping hole and a slagging hole for discharging steel water and slag, respectively.
Process Flow of Converter Steelmaking
The process flow of converter steelmaking includes the following main steps:
Preparation of Raw Materials: This includes molten iron, scrap steel, ferroalloys, and slagging materials. Molten iron is the main raw material for converter steelmaking, while scrap steel and ferroalloys are used to adjust the composition of the steel water. Slagging materials are used for slagging to remove impurities in the molten iron.
Blowing: After loading the raw materials such as molten iron and scrap steel into the converter, oxygen or other oxidizing gases are blown in for blowing. During the blowing process, impurity elements in the molten iron are oxidized to generate oxides that enter the slag, while releasing a large amount of heat to increase the temperature of the molten bath.
Slagging: During the blowing process, slagging materials (such as limestone and dolomite) are added to react with impurity elements in the molten iron to generate slag. The slag can adsorb and remove impurity elements from the molten iron, thereby improving the quality of the steel water.
Tapping of Steel and Slag: When the composition and temperature of the steel water meet the requirements, the blowing is stopped, and the converter is tilted to discharge the steel water from the tapping hole. Simultaneously, the slag is discharged from the slagging hole.
Refining and Casting: Depending on the needs, further refining processes (such as deoxidization, desulfurization, and degassing) can be performed on the steel water, followed by casting into steel billets or ingots.
Technical Characteristics of Converter Steelmaking
Efficiency: Converter steelmaking is a large-scale, continuous production method with high production efficiency.
Flexibility: Converter steelmaking can adjust blowing parameters and slagging systems according to different raw material conditions and production requirements to adapt to different production conditions.
Environmental Protection: With the increasing awareness of environmental protection, converter steelmaking also faces increasingly stringent environmental requirements. By adopting advanced dust removal, desulfurization, and denitrification technologies, pollution emissions during converter steelmaking can be reduced.








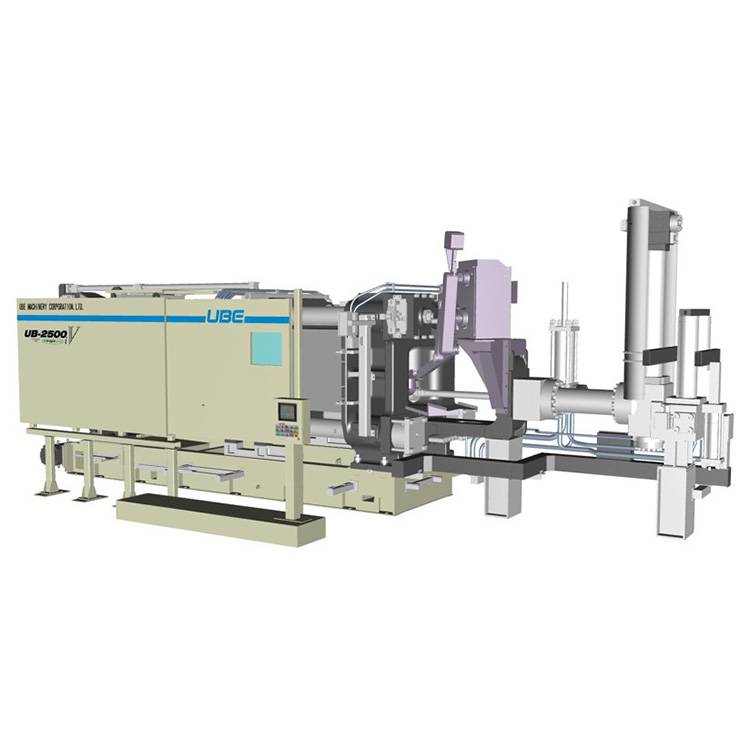
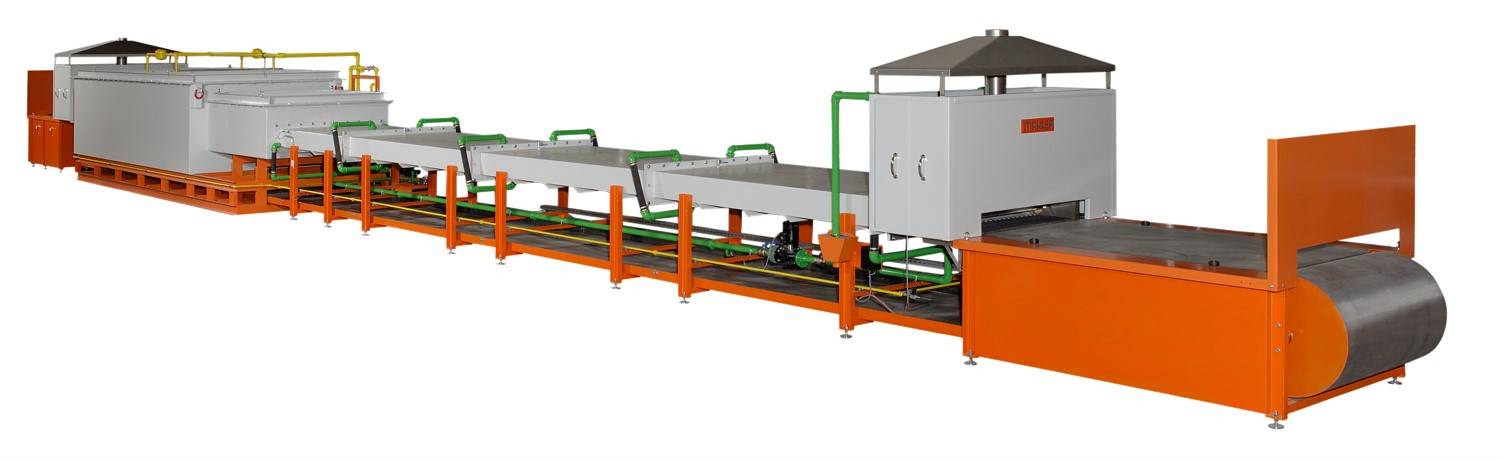
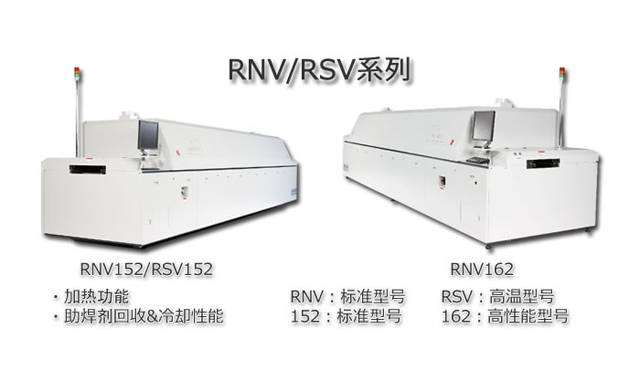
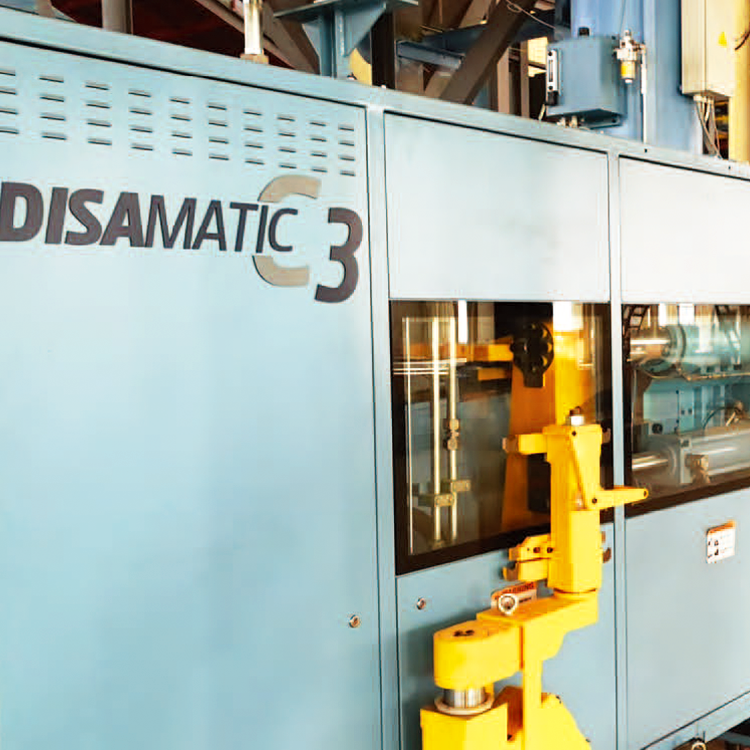
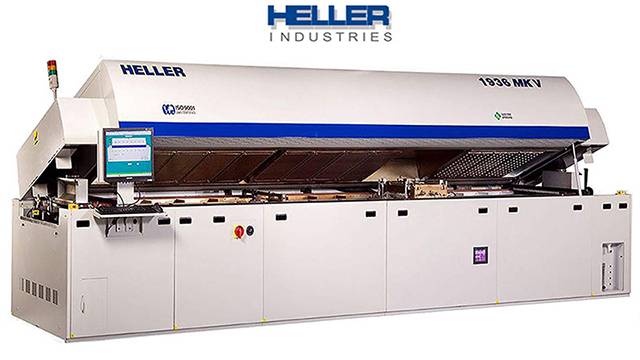
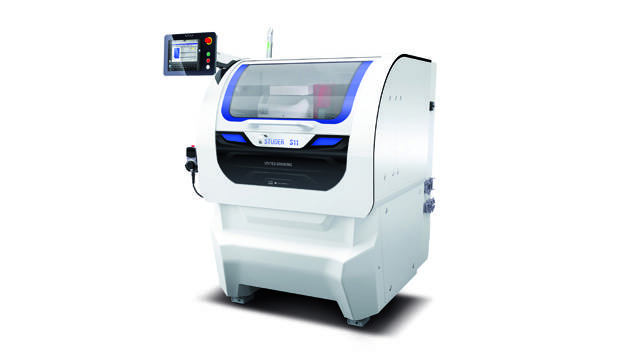
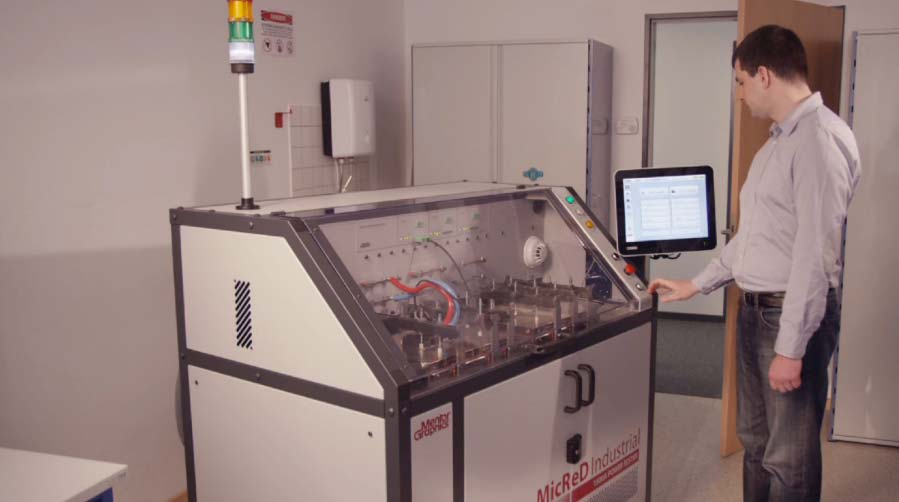
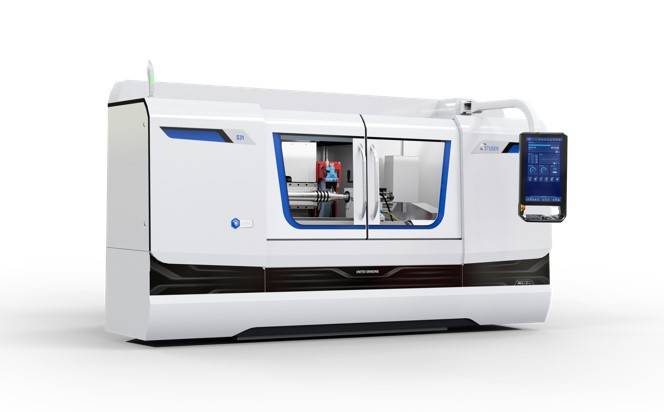
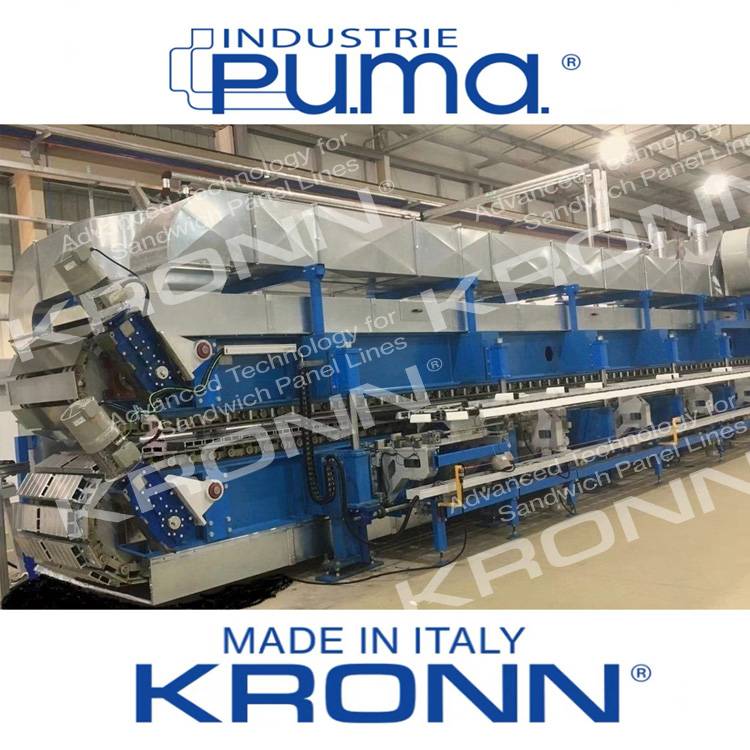
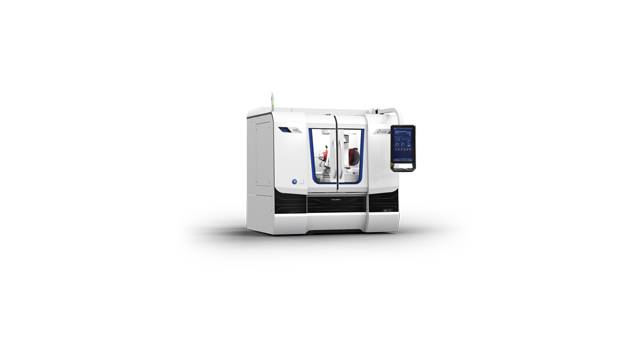